Epoxy Resins
ebalta epoxy resins are two-component systems that cover a very wide range of applications: for mould and tool making – in addition to the ebaoard epoxy boards – modelling pastes, epoxy casting resins, gel coats and reinforcing pastes are offered.
Due to their high strength and high heat resistance, ebalta’s general-purpose and laminating resins are suitable for the production of composite parts, laminate moulds, backfillings or as binding resins for fillers. Due to the varied choice of hardeners, pot life can be optimally adjusted. The result: dense surfaces and stable components.
The great advantage of ebalta’s diverse epoxy product range is that they are precisely tailored epoxy resin systems that are used for parts and mould and tool construction.
Modelling Paste
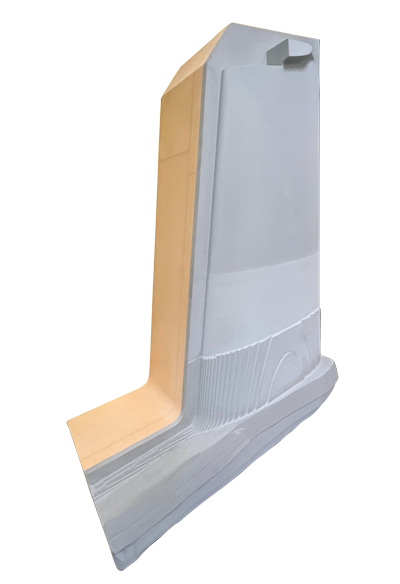
Especially for large design models and extensive laminating moulds, the machine-processable epoxy mould making pastes from ebalta are a guarantee for seamless and dense surfaces.
The mould making pastes are very dimensionally accurate and stable. They are very easy to apply and allow layer thicknesses of 15-35 mm in one process. The low exotherm and the easy milling processes give a perfect result for jointless models and moulds in automotive, boat building, aircraft construction or wind power.
Epoxy lay-up pastes from ebalta are always a good choice for quick fabrications or changes to the model and mould at comparatively low cost.
In Addition, a modelling paste team is available to apply the modelling paste to a base with their own machine on site or on the ebalta production halls.
Product | Density (at 20°C) | Heat resistance | ||
---|---|---|---|---|
P 22 / P 22 | ||||
P 28 / resin + hardener | ||||
P 29 / resin + hardener | 0.77 ± 0.03 g/cm³ | 87°C |
Epoxy Casting Resins

ebalta epoxy casting resins are the preferred products for extensive models and moulds with high precision. The EP casting resins from ebalta have compressive strength and high heat resistance. This makes them suitable for vacuum forming moulds, PU and RIM foam moulds but also as heatable foundry patterns requiring high dimensional accuracy and low sand adhesion. The resins are very pleasant to work with and are characterised by very low shrinkage. At the same time, ebalta epoxy casting resins are very abrasion-resistant, chemical-resistant, easy to polish and have a dense surface.
Which EP casting resin is suitable for the production of cast models and moulds depends on model size and number of pieces. Even very large quantities can be produced reliably and user-friendly with ebalta epoxy casting resins, whether in solid casting, front layer casting or build-up processes.
Product | Heat resistance (HDT) | ||
---|---|---|---|
GH 705 / TL-1 | 91 ± 3 °C | ||
GH 706 / GL | 67 ± 2 °C | ||
GH 730 / BR | 64 ± 2 °C | ||
GH 752 / TL-1 | 90 ± 3 °C | ||
GH 760 / GL | 63 ± 2 °C |
General Purpose & Laminating Resins
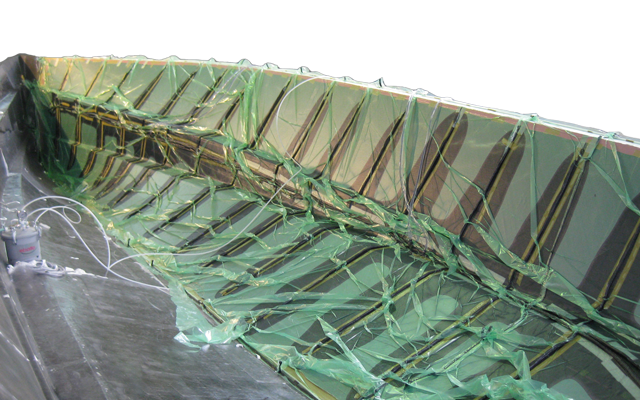
ebalta all-purpose resins and laminating resins are ideally suited for extensive tools and parts with high accuracy. They are very comfortable to work with and are characterised by very low shrinkage. The wide range of epoxy hardeners makes it possible to adjust the pot life and thus optimise the working process. Particularly worth mentioning is the flame-retardant laminating resin LH 25 for dimensionally accurate parts according to DIN 5510-2.
The temperature-resistant all-purpose resin and laminating resin systems are used for moulds in vehicle, aircraft and boat construction, both for manual lamination and for the vacuum infusion process. With vacuum infusion, a higher fibre or lower resin content is achieved for the same component weight. The ebalta general purpose resins including vacuum infusion accessories are optimally adjusted to the vacuum infusion process. Appropriate training is offered by the product management team.
Product | Heat resistance (HDT) | Pot life 200 g / 20 °C | ||
---|---|---|---|---|
AH 100 / D | 58 ± 3 °C | 45 - 55 min. | ||
AH 100 / GL | 60 ± 3 °C | 45 - 55 min. | ||
AH 100 / TG | 75 ± 3 °C | 40 - 50 min. | ||
AH 100 / TGL | 76 ± 2 °C | 65 - 75 min. | ||
AH 100 / TGS | 76 ± 3 °C | 25 - 35 min. | ||
AH 110 / GL | 75 ± 3 °C | 40 - 50 min. | ||
AH 110 / LI 20-1 | 98 ± 3 °C | 20 - 25 min. | ||
AH 110 / TG | 100 ± 3 °C | 35 - 40 min. | ||
AH 110 / TGL | 101 ± 3 °C | 55 - 65 min. | ||
AH 110 / TGS | 99 ± 3 °C | 20 - 25 min. | ||
AH 110 / TL-1 | 105 ± 3 °C | 85 - 95 min. | ||
AH 120 / GL | 63 ± 2 °C | 40 - 45 min. | ||
AH 120 / LI 130-2 | 100 ± 3 °C | 140 - 160 min. | ||
AH 120 / LI 20-1 | 81 ± 3 °C | 20 - 25 min. | ||
AH 120 / TC 60 | 102 ± 3 °C | 60 - 70 min. | ||
AH 120 / TG | 93 ± 3 °C | 35 - 40 min. | ||
AH 120 / TGL | 97 ± 3 °C | 60 - 70 min. | ||
AH 120 / TGS | 91 ± 3 °C | 20 - 25 min. | ||
AH 120 / TL-1 | 100 ± 3 °C | 80 - 90 min. | ||
AH 140 / LI 130-2 | 107 ± 3 °C | 120 - 140 min. | ||
AH 140 / LI 20 | 91 ± 3 °C | 18 - 22 min. | ||
AH 140 / TC 60 | 97 ± 3 °C | 55 - 65 min. | ||
AH 140 / TC 90-2 | 110 ± 3 °C | 90 - 105 min. | ||
AH 150 / IP 25 | 80 ± 3 °C | 15 - 25 min. | ||
AH 150 / IP 430 | 79 ± 3 °C | 300 - 430 min. | ||
AH 150 / IP 55 | 78 ± 3 °C | 50 - 60 min. | ||
IH 16 / hardener fast | 78 ± 3 °C | 50 - 60 min. | ||
IH 16 / hardener slow | 79 ± 3 °C | 300 - 400 min. | ||
LH 22 / GL | 64 ± 2 °C | 40 - 45 min. | ||
LH 25 / Resin+Hardener | 90 ± 3 °C | 50 - 60 min. | ||
LH 28-1 / TM | 175 ± 3 °C | 240 - 360 min. | ||
LH 30 / Resin+Hardener | 181 ± 5 °C | 160 - 200 min. |
Gel Coats
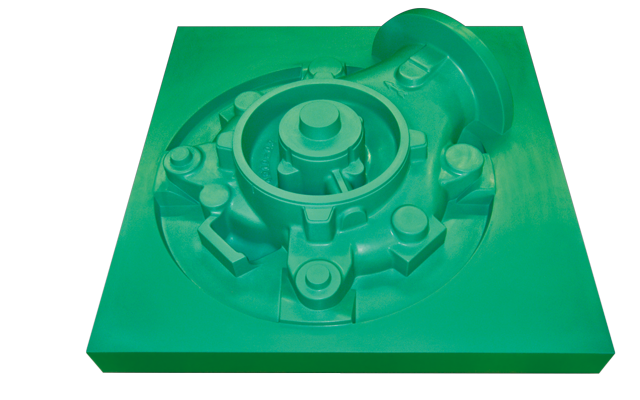
The surface resins or gel coats from ebalta are essential in the production of negatives, master models, jigs or foundry patterns. They are used, for example, in the build-up process of extensive models made of gelcoat, following coupling paste and a corresponding resin rear frame. The versatile products can be used universally and are very easy to spread. Depending on the requirements, models and moulds made of ebalta gel coats are easy to grind, polishable, resistant to chemicals and very dimensionally accurate. ebalta offers surface resins for highly abrasion-resistant models and moulds, and dense or impact-resistant surfaces.
In addition to the epoxy gel coats, the polyurethane surface resins OH 11 / PUR 3 and OH 11 – hard / PUR 1 are offered.
EP gel coats | Heat resistance (HDT) | ||
---|---|---|---|
OH 33 / H 2017 | 100 ± 3 °C | ||
OH 38 / H 2017 | 104 ± 3 °C | ||
OH 38 / HM | 145 ± 5 °C | ||
OH 4 / H 2017 | 85 ± 5 °C | ||
OH 6-1 / H 2017 | 101 ± 3 °C | ||
OH 82 / TM | 175 ± 5 °C |
PU surface resins | Heat resistance (HDT) | ||
---|---|---|---|
OH 11 – hard / PUR 1 | 70 ± 2 °C | ||
OH 11 / PUR 3 | 70 ± 2 °C | ||
OH 49-1 / Comp. A+B | - |
Reinforcing Pastes
The glass fibre-containing two-component reinforcing pastes from ebalta on an epoxy resin basis impress with their smooth and temperature-resistant processability. Classically, ebalta EP reinforcing pastes are used as reinforcement for foundry patterns and in core boxes. It is precisely their low specific weight that makes ebalta laminate pastes suitable for the lightweight construction of extensive reinforcements. In the laminate paste systems, the laminate paste, which contains glass fibres and other reinforcing materials, is particularly easy to mix with the coloured hardener. The mixture is easy to apply and cures at room temperature without significant shrinkage. After curing, it has very good strength. For vacuum forming tool applications PS 08/TL-1 is used. This is a glass-fibre and aluminium-containing temperature-resistant two-component epoxy resin that is breathable.
Product | Density (at 20°C) | Heat resistance | ||
---|---|---|---|---|
PS 02 / BRI | 1.05 ± 0.02 g/cm³ | 40 ± 2 °C | ||
PS 02 / BRIL | 1.05 ± 0.02 g/cm³ | 40 ± 2 °C | ||
PS 03-1 / PS 03-1 L | 0,96 ± 0,03 g/cm³ | 68 ± 2 °C | ||
PS 05 / TL-1 | 1,10 ± 0,05 g/cm³ | 105 ± 5 °C | ||
PS 08 / TL-1 | 1,75 ± 0,05 g/cm³ | 80 ± 3 °C |