Sustainable plastics as a research focus
German companies spent 88.7 billion euros on research and development (R&D) in 2023 – and the trend is rising. This is according to the R&D survey conducted annually by the Stifterverband on behalf of the Federal Ministry of Education and Research. This is encouraging and good for Germany as a business location. ebalta Kunststoff GmbH is also making an important contribution to this. Ten specialists from the company, which employs around 130 people in total, are driving forward the development of new plastic products in the in-house laboratory. This commitment has now been officially confirmed by the seal of the Certification Centre for Research Allowance (BSFZ). The centre checks whether a company conducts research and development and is therefore entitled to a research allowance from the federal government.
Sustainability as the most important topic
ebalta has been investing in its own development department since 1998. Initially, existing products were modelled there, but over time the focus shifted more and more to in-house developments. ‘Our most important topic today is sustainability,’ explains Clemens Saalbach, Head of Development at ebalta. ‘In the past, our products were made almost exclusively from fossil fuels. For some years now, we have been working intensively on the use of renewable raw materials – with success.’ This means that ebalta products can now also be made partly from vegetable oils, such as castor or sunflower oil, or even sugar. ‘The challenge here is that this plastic must have the same properties as before. The customer must be able to rely on this,’ emphasises Clemens Saalbach. However, the properties of natural products fluctuate more than those of conventional raw materials. For this reason, his team invests a large part of its capacity in the precise research of these natural raw materials and their implementation in ebalta products.
Cost-intensive investment
The process is complex: Firstly, the properties of the raw material are tested, then its reaction is tested when mixed with another ingredient. The corresponding mixtures must be moulded, cured and tested for hardness, elongation, heat resistance, etc. The recipe is then adjusted and the process repeated until the result meets the quality specifications for the desired product. ebalta’s production area is an important partner for the developers: ‘You can think of the production of a plastic as the realisation of a cooking or baking recipe,’ explains Clemens Saalbach. ‘Step by step, the ingredients are added to the pot and mixed. The quantity and production conditions play an important role here. For example, a product may behave differently if it is produced in large quantities.’ This also needs to be checked and tested for the final product, after which the recipe is refined again if necessary.
This development process can take several months under certain circumstances. It is time-consuming, but also costly in terms of personnel, purchasing, testing and maintenance of expensive technical equipment, consumables, and so on. This adds up to quite a lot before the product is ready for the market and can generate sales. ‘As a medium-sized company, we are therefore happy about the opportunities for financial support from the federal government, for example through the research allowance,’ says Clemens Saalbach.
Innovative plastics developments
In recent years, ebalta has launched promising new developments in the field of sustainability: duranity©, a polyurethane casting resin for the production of climbing holds, which consists of around 40 per cent raw materials from renewable sources. And ‘The Green Stuff’, also a polyurethane plastic with up to 65 per cent sustainable raw materials, which is primarily used in toolmaking, for example as a model in foundries.
In addition to developing new products, the R&D team at ebalta also works on adapting products as part of the product life cycle or uses all its creative energy and expertise to realise special customer requests. ‘We serve very different industries and produce rings for computer tomographs, for example. We have also developed a casting resin that enables the flush installation of laminate worktops,’ says Clemens Saalbach. Some of the employees in the laboratory team are also responsible for continuous quality assurance and regular testing of the technical instruments.
Curiosity as an important driver
Customers with special tasks always provide new and exciting challenges. ‘Sometimes the client themselves cannot define exactly what properties the new plastic must have for their purposes,’ explains Clemens Saalbach. ‘In order to find a solution, our flexibility and creativity as well as our understanding of the product are required. This is exactly what makes our work so appealing: We approach these challenges with an open mind and great curiosity and look forward to realising them.’
For more information on ebalta’s development of sustainable plastics please go to https://ebalta.com/en/plastics-development/
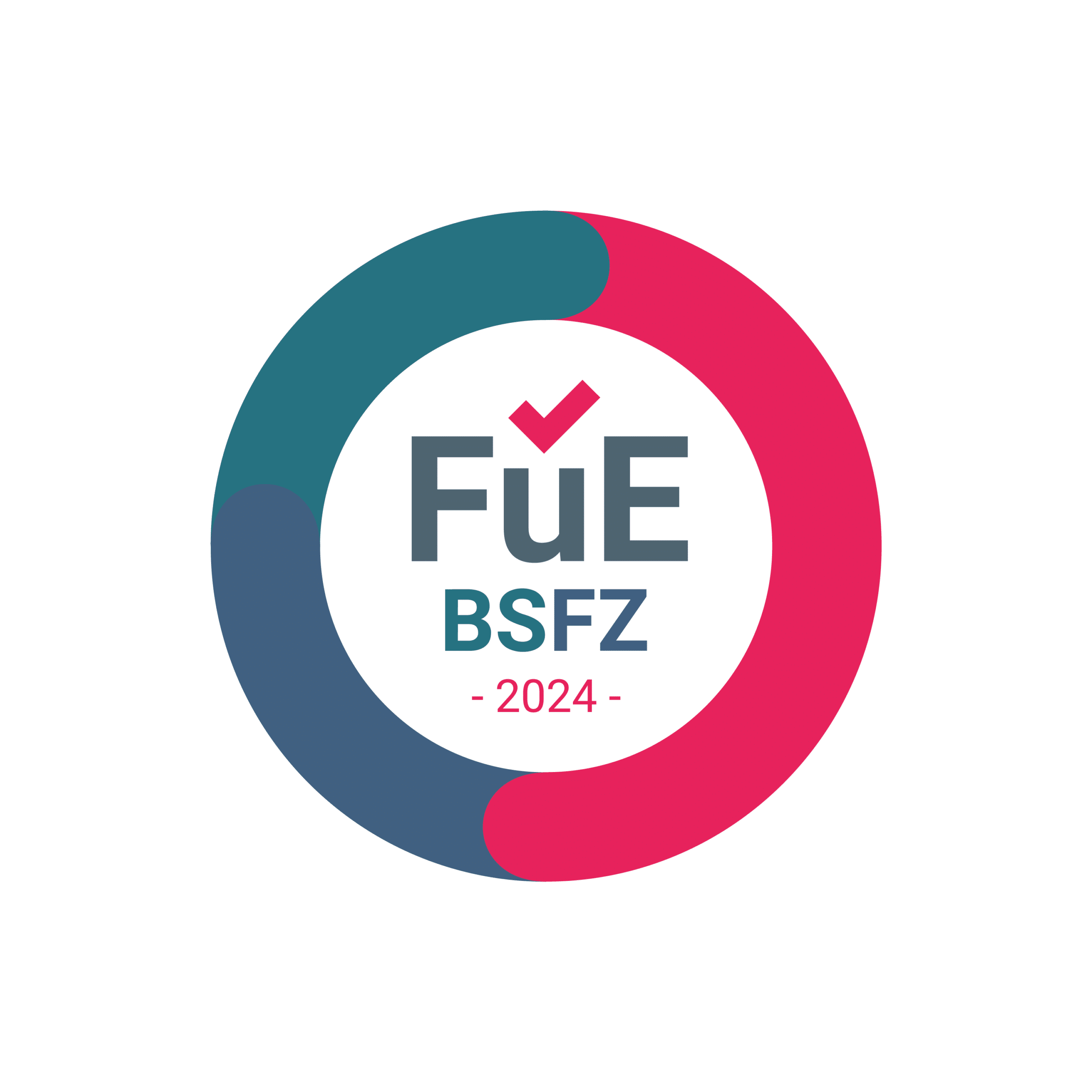
ebalta received the seal of approval from the Research Grant Certification Centre (BSFZ) for the year 2024.